Type N
Since Sunkid was founded in 1996, the optimization of existing and the development of new transport solutions has been a central area of the company. In close cooperation with customers, research institutes, and specialized partner companies, Sunkid can continue to offer even better passenger transport solutions in the future. In recent years, for example, a great deal has been invested in the new and further development of conveyor belts. In 2022, Sunkid will be presenting a completely new generation of its conveyor belt - the Type N.
The Type N - Ready for the new generation
The Type N sets a new standard in passenger transportation. It combines top quality with optimum resource utilization and maximum user-friendliness. In addition, the newly integrated switchgear offers a new usability concept and sets new standards in terms of maintenance and operation of the system. The Type N also complies with all current regulations of the authorities worldwide.
Maximum user-friendliness with i-CONTROL® switchgear:
The heart of the Type N is the new i-CONTROL® electrical control system. This new control system was already intensively tested on several lifts in the winter of 2020/21 and has been used by Sunkid as standard on all lifts in the Alpine region since this winter 2021/22. The newly developed operating system displays the current operating status clearly and concisely and guides the user easily through all functions.
The key features of i-CONTROL®:
- Multi-touch HMI (display) with all relevant information for operation, maintenance and troubleshooting
- Including 4 different password-protected user groups, each with a defined release of functions
- Including digital (documented) maintenance plan of the plant
- Remote access to the electrical control system via internet for customer and manufacturer (for extended customer support)
- Regular reports by e-mail on the most important operating data (such as utilization, etc.) to various recipients (customer or manufacturer)
- The new Type N conveyor generation was first presented to the public by Sunkid at the Mountain Planet trade fair in Grenoble. However, numerous installations have already been running in the Alpine region since the 2021/22 winter season
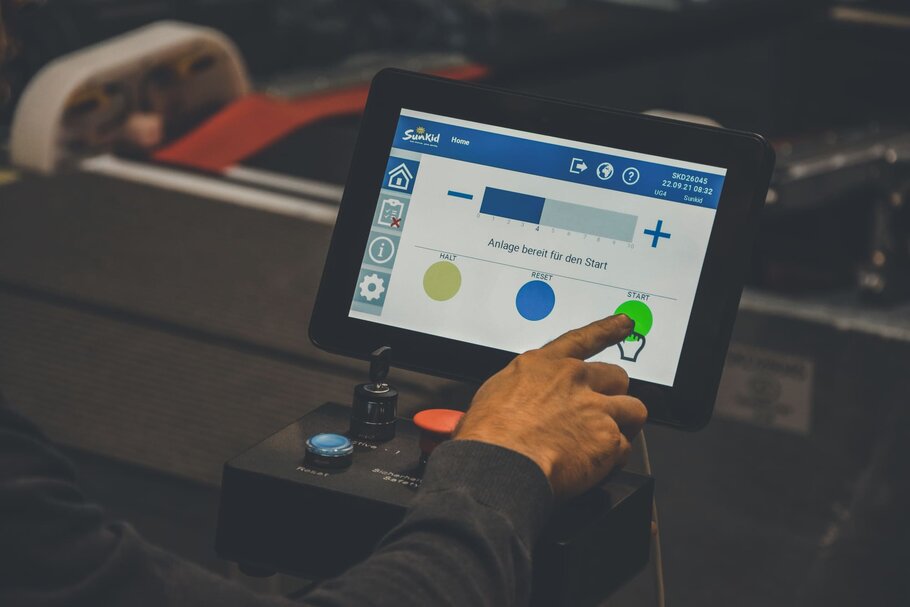
Sustainable logistics solution
In recent years, there have always been different designs and product types. Due to this design breadth and depth, on the one hand the production of new systems was correspondingly costly and on the other hand, of course, the spare parts system was also very extensive. With the completely newly developed Type N, a uniform standard was created with which Sunkid can cover the entire range of applications (ski conveyors, logistics solutions, summer applications, water conveyors, etc.) in all variants. This allows for faster project implementation times, reduced number of components, and easier lifetime customer support of a system. In addition, the new components are even more stackable and can therefore be transported more compactly and with fewer truck-load meters. The development incorporates 25 years of know-how from more than 3,900 installations worldwide. For example, a newly designed plastic slide table ensures a reduction in friction and suction between the conveyor belt and the running surface. Channels running out to the side also allow easy water drainage. Lateral conveyor belt guide rollers guarantee clean belt tracking and optimize wear on the conveyor belt side. Integrated cable trays and additional storage spaces at the top and bottom stations ensure clean cable routing and protection from environmental influences. The roofing solutions for the conveyor belts have also been further developed and fit seamlessly into the new Type N generation with innovative design solutions.
THE CONSTRUCTION:
Drive Station
During development, the highest attention was paid to safety for passengers but also for maintenance personnel. For example, the cover for the double light barrier at the exit is shaped to minimize the risk of objects getting caught. All covers, both at the top and bottom stations, are equipped with safety sensors and stop the installation immediately as soon as a cover is opened in normal operating mode. A special enabling switch allows the system to be operated easily and safely by the operating personnel in maintenance mode. The system can be easily and safely operated by the operating personnel in maintenance mode via a special enabling switch.Direct mounting of the motor and gear unit. Motorization of the system adapted to the length, gradient and load of the system depending on the project. Diameter of drive drum between 300mm and 600mm, depending on drive power, with trapezoidal running contour, which keeps the conveyor belt in central position even in inclined position. Adjustable deflection roller ensures higher wrap angle of the conveyor belt and thus even more friction. Motorized rotating cleaning brush underneath the conveyor belt allows easy cleaning of the conveyor belt surface.
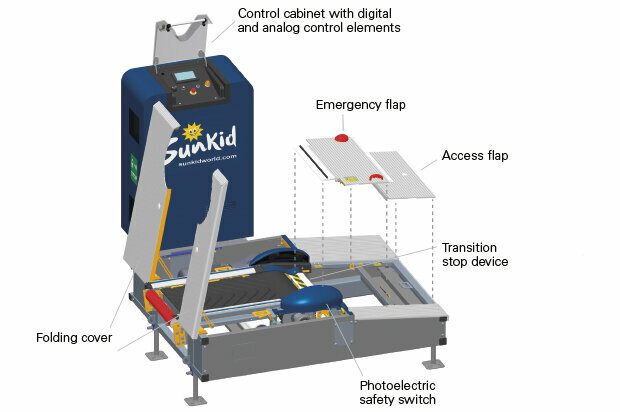
Control cabinet
The heart of the Type N is the new i-CONTROL® electrical control system. This new control system was already intensively tested on several lifts in winter 2020/21 and has been used by Sunkid as standard on all lifts in the Alpine region since winter 2021/22. The newly developed operating system displays the current operating status clearly and concisely and guides the user easily through all functions.
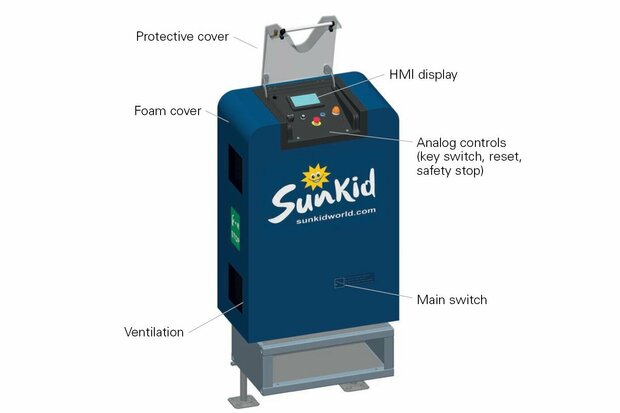
Mid section
Newly designed, uniform and weight-optimized center segments (in 4 or 2 meter modules) significantly facilitate on-site assembly. For example, new hook systems and connecting plates between and on the segments ensure even easier assembly and reduced use of personnel and tools. Integrated cable tray protects cabling from environmental influences and ensures tidy cable routing. Fan rollers at each transition reduce conveyor belt friction forces. Special V-Slide sliding table in polyethylene reduces friction and suction on the running surface, ensuring longer belt life. It also prevents the conveyor belt from freezing on the sliding surface and drains off any melt water that arises via outflowing channels.
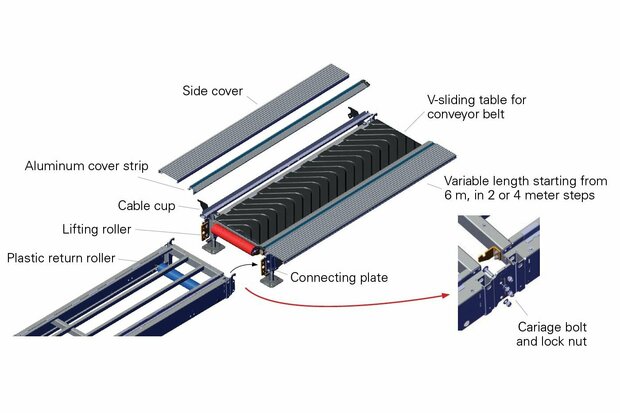
Side Cover
Another highlight is the conveyor belt cover bar made of aluminum, which is height-adjustable in 5 steps and thus enables the perfect closure between belt and cover. This all has the effect of reducing friction, which in turn reduces energy consumption. It also ensures an even longer service life of the system. Integrated H-plastic bar ensures reduction of friction on the belt surface. Lateral guide rollers reduce the frictional forces of the conveyor belt and serve to center the conveyor belt more precisely.
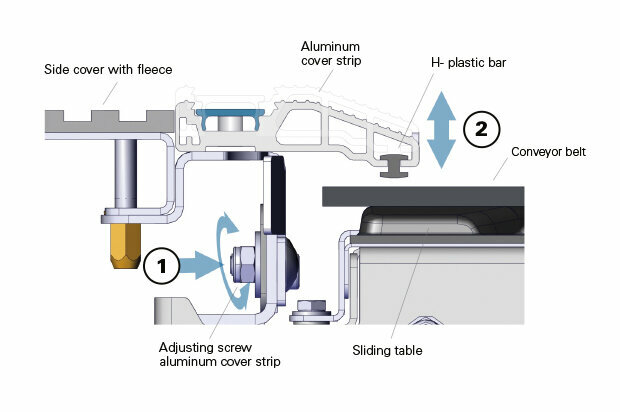
Hydraulic Diverter Jumbo
Metal covers that swing open at the sides provide easy and quick access for maintenance tasks. All covers are monitored with safety sensors. Hydraulic clamping unit with a clamping travel of 100 cm. Deflection roller with a diameter of 290 mm and trapezoidal running contour keeps the conveyor belt in central position even when inclined. Separate flywheel gearbox ensures smooth belt running. Adjustable entrance plate adapts entrance area to the terrain. A special enabling switch allows the system to be easily and safely operated by the operator during maintenance.
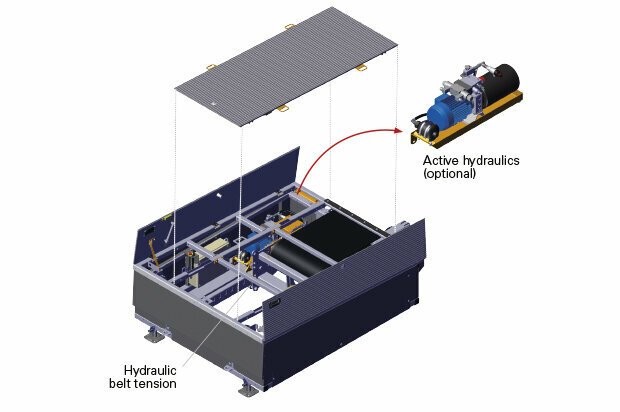
Media library
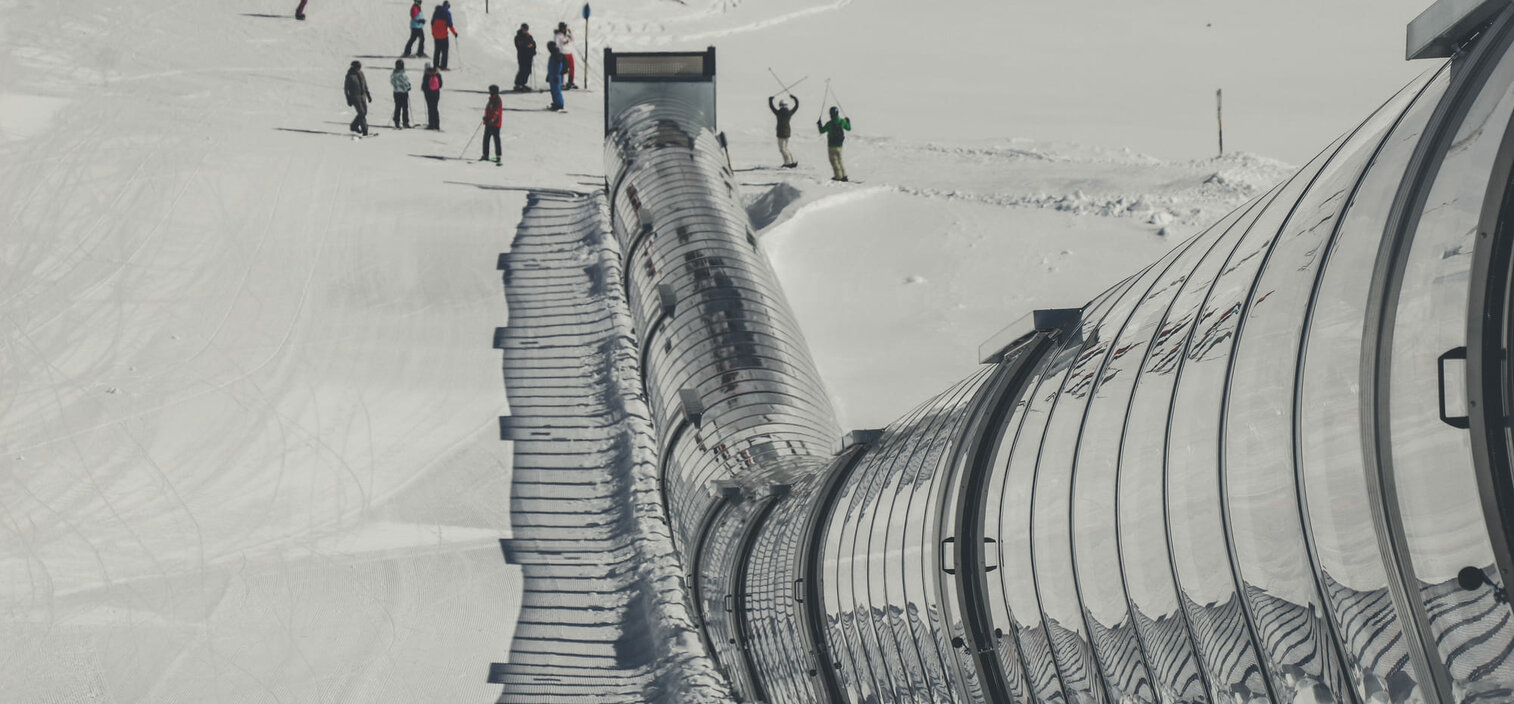
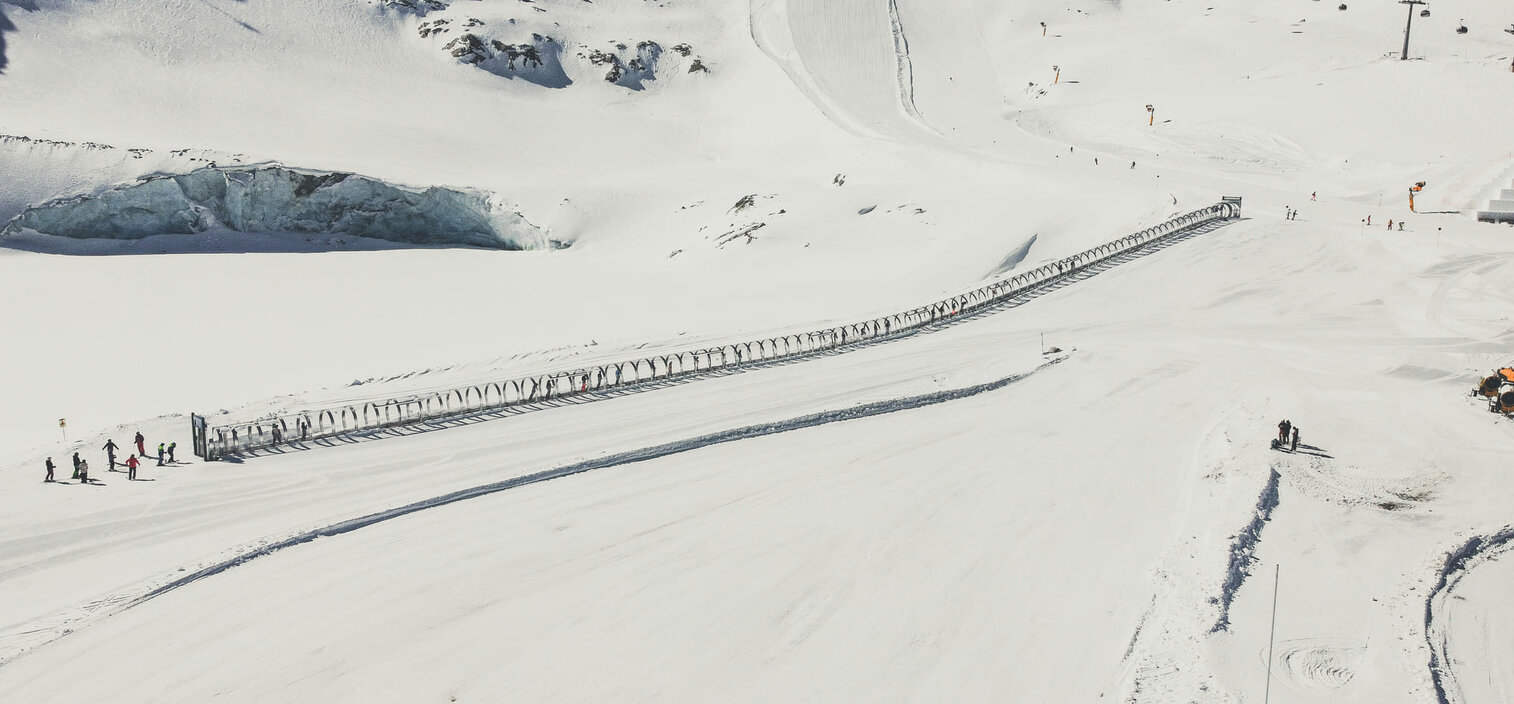
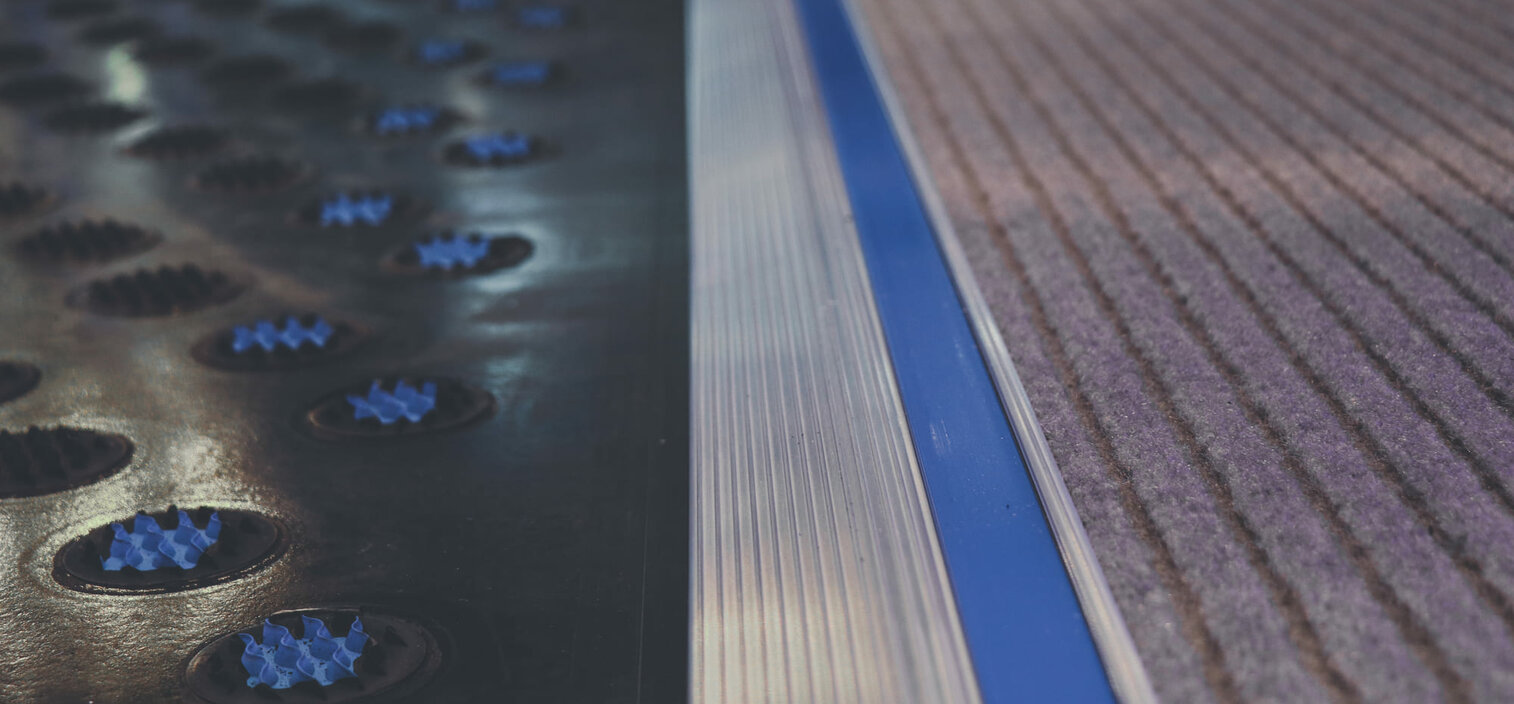
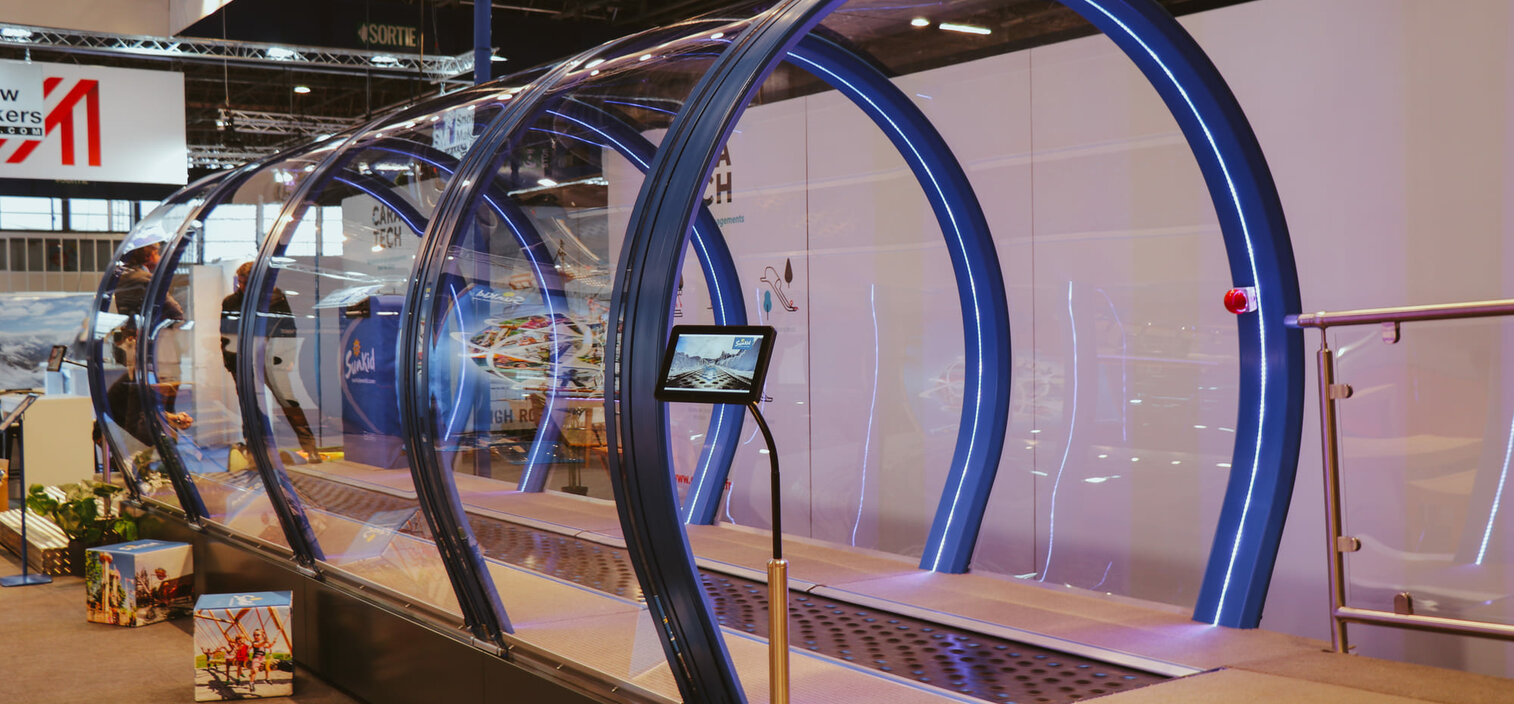
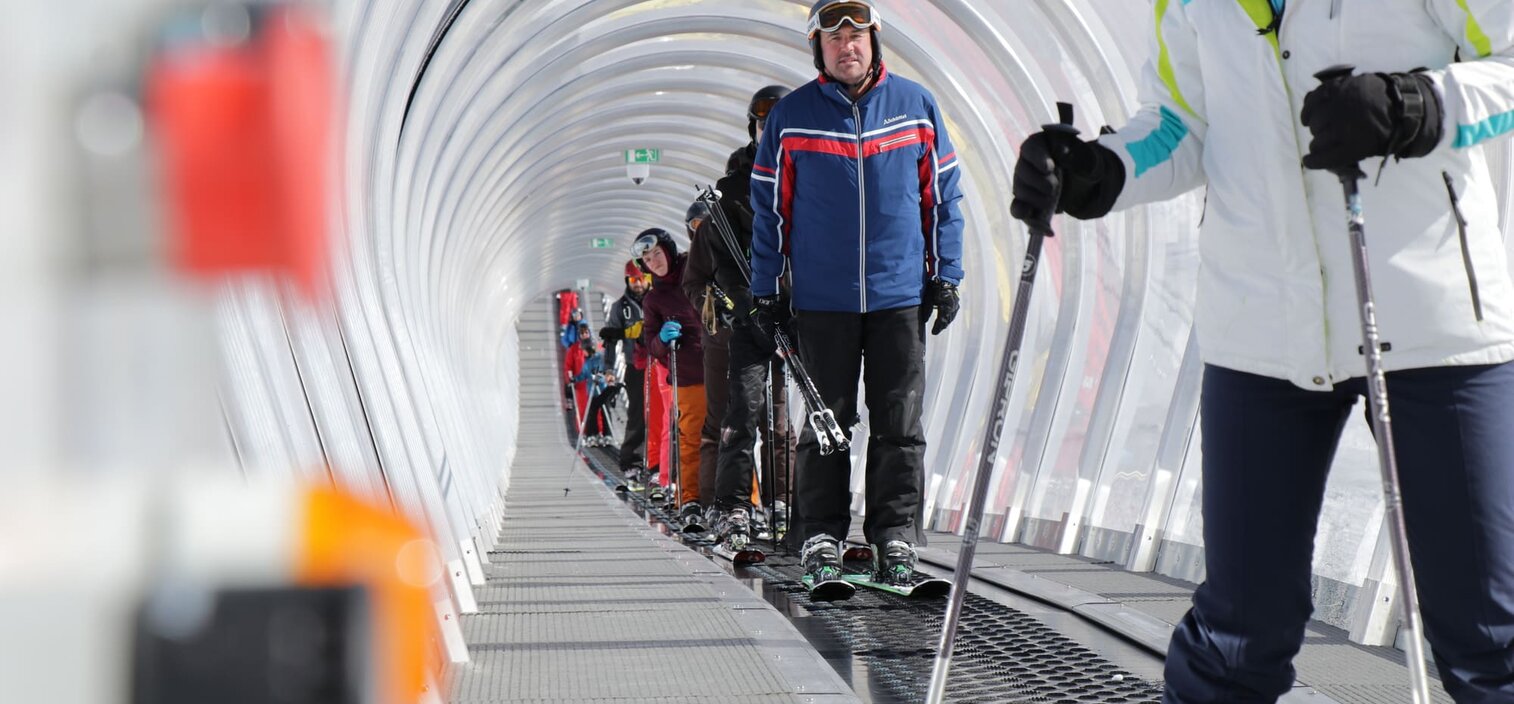
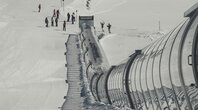
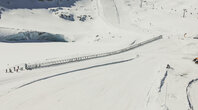
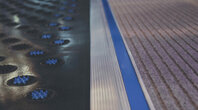
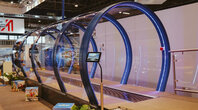
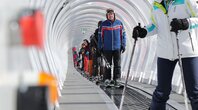